How are boxing gloves made?
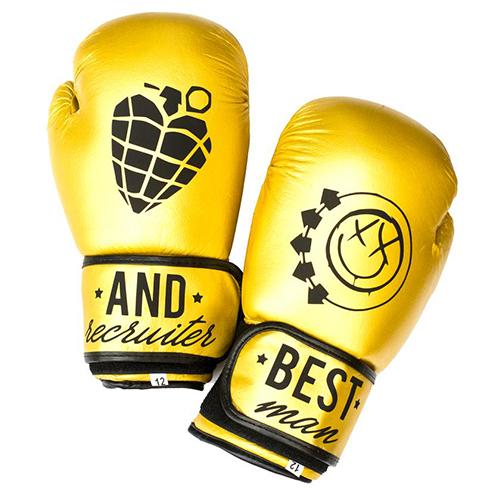
How are Leather boxing gloves made?
Fist fighting has existed as a form of human entertainment since the earliest days of human civilization. Some form of the sport appeared as long as six thousand years ago in what is now known as Ethiopia before it spread across the ancient world. Throughout the history of the sport, segments of society deemed that it was too brutal and have lobbied to restrict or ban it altogether. Partly in deference to those efforts and partly in recognition of the frailty of the human body, practitioners and promoters have developed defences for use in the sport. The oldest and most little changed of these has been the boxing glove.
History
It is generally acknowledged that the inventor of the modern day boxing glove was an English champion fighter who went by the name of Jack Broughton. Jack fought, as did all boxers of his day, with bare knuckles. Jack developed his gloves—now known as mufflers—so that the gentry could practice boxing at the gymnasium without inflicting serious damage on his peers. The gloves were reserved for such uses and all public contests were still fought with bare fists. In 1743, Jack codified the first modern rules of boxing. Then in 1867, John Graham Chambers, a member of London's Amateur Athletic Club, published the Marquis of Queensberry rules. Line eight of the rules read, "The gloves to be fair-sized boxing gloves of the best quality, and new." The rules were gradually adopted for amateur competition, and the use of thinly padded or skintight leather mitts became more widespread. Still, most public and professional bouts were fought with bare knuckles.
American fighter John L. Sullivan is said to have been one of first to popularize the wearing of gloves in public fights. Sullivan reigned as World Heavyweight Champion from 1882-1892, but many historians do not consider him to be the first modern champion as all the fights in which he won his title were waged under the old Prize Ring rules, which did not require gloves. Ironically, Sullivan did wear gloves in his last fight, in which he lost to the first champion under the Marquis of Queensberry Rules, James "Gentleman Jim" Corbett.
Raw Materials
The skin of a boxing glove is top grain tanned leather, most often cowhide or goatskin because of their durability and flexibility. Lesser-quality gloves will be made from vinyl, but most sanctioning bodies—amateur and professional—require leather gloves. Some manufacturers line their gloves with another layer of leather, but the majority use nylon taffeta. Gloves are stitched with nylon thread and padding is of high-density polyurethane,
Latex, or polyvinyl chloride (PVC) foam delivered in sheet form. Historically, cotton batting has been used as padding and many manufacturers still use this material to pad some portion of their models. Some manufacturers also use horsehair.
Design
The primary design consideration involves the glove's padding. In order for a padding material to be effective, it must absorb energy by compressing. The more it compresses, the more energy it absorbs. If a material compresses too much, it ceases to be useful because it becomes simply a thin layer of dense material. Partly because of this, different weight classes require gloves of different weights. A glove's weight is changed by adding or removing layers of padding. If the same glove weight was required for all weight classes, blows thrown by the largest and heaviest boxers would compress the padding beyond its useful range, while blows thrown by the lightest boxers would barely compress the material at all. In addition, many materials that offer excellent energy absorption also display a characteristic known as memory. Once compressed, these materials maintain their deformed state for an extended period of time so that the initial blow with a glove offers normal protection, but subsequent blows are virtually unpadded.
Other design criteria stem from rules and regulations of the various sanctioning bodies. For example, USA Boxing, which regulates much of the amateur competition in the United States and sanctions all Olympic-style competition in the United States, requires that all gloves either be thumbless or have the thumb compartment attached to the body of the glove so that boxers cannot jab each other in the eye. In addition, gloves used for international competition, such as the Olympics, must have a portion of the leather covering the knuckle area dyed white for scoring purposes.
The Manufacturing Process
Patterns and cutting
All boxing gloves are cut, assembled, stitched, stuffed, and finished by hand. The manufacture of a glove begins with a pattern of the individual pieces. While every manufacturer has a different pattern, the basic pieces are the palm, which is cut with a slit down its middle that will eventually form the closure section of the glove; the knuckle area, which is always made from a single piece of leather to avoid seams; the thumb, which is made from two halves; the cuff, which is cut as a wide strip; and a thin strip that will be folded over and sewn onto the edge of the cuff and the closure area to finish the glove. The knuckle piece is cut to be larger than its finished size so that space is left for stuffing.
- 1 Leather arrives from the tannery in large pieces and is laid out on large cutting tables. The patterns are placed on the leather and arranged to make the most efficient use of that piece. The patterns are then traced onto the leather and the pieces are cut with large scissors. Meanwhile, similar patterns are traced onto the lining material and those pieces are cut. Pieces are made to line the palm, the thumb, the cuff, and the knuckle area.
Assembly and stitching
- 2 The leather shell of a boxing glove is first sewn together inside out. Stitching is often done on an industrial sewing machine with some of the smaller pieces and finishing work being completed by hand. Many of the higher quality gloves are stitched entirely by hand, and double stitching is used throughout all quality gloves.
- 3 The oversized knuckle piece is stitched to the palm piece. The two pieces are fitted over a buck to assure the correct shape and the seam is gathered so that the knuckle piece balloons slightly. Gathering the seam also causes the glove to take on its trademark clenched fist shape.
- 4 Then, the liner pieces are stitched onto this assembled section and the palm is stuffed with padding. The liner is left open at the bottom of the glove, where the cuff will be attached. On many models, the back halves of the thumb pieare is cut as part of the knuckle piece, and the inner half is sewn onto the knuckle and palm pieces. On others, the thumb is stitched together separately; its lining is attached, and its padding is stuffed. The assembled thumb piece is then stitched onto the glove.
Stuffing the glove
- 5 The entire glove assembly is now turned right side out. As it is more economical for manufacturers to purchase padding material in standard sheet form, the padding for the knuckle area is made by layering sheets of the material and then cutting it to the desired shape. This also allows glove makers to use one standardized thickness of padding for many glove weights and specifications rather than purchasing or manufacturing a different molded piece for every glove model.
- 6 The pattern for the glove being made is traced onto the padding material and it is cut. Depending on the manufacturer, pattern pieces may be cut in mass beforehand and kept in stock for assembly.
- 7 The cut pieces are layered to the specified thickness and are stuffed into the pocket between the knuckle area and its lining.
- 8 The last piece to be stitched to the glove is the cuff. The cuff and its lining are stitched together, and the piece is stuffed. The ends of this assembly are not stitched together as the piece will eventually form part of the gloves closure area.
- 9 The assembly is stitched to the open end of the glove piece, closing off all the open pockets and sealing the glove's padding.
- 10 On If the glove is to be closed with laces, a template is laid over the opening now formed on the glove's underside by the slit in the palm and the open ends of the cuff, and laces holes are punched with an awl. Each hole is strengthened with stitching, and the entire lace area is finished with several rows of stitching.
- 11 If the gloves are to be closed with hook and loop material, the loop side is sewn onto the outside face of the cuff, and the hook side is stitched onto the cuff's opposite edge.
- 12 A single thin strip of leather is folded over the open edge of the cuff and the lace area and is stitched in place to finish the glove. The maker's label and any required sanctioning body labels are sewn onto the back of the cuff and the finished gloves are packaged for shipping.
The Future
The most surprising aspect of boxing gloves is how little they have changed. The first gloves were leather mitts with little or no padding. Today's gloves have added padding to a greater or lesser degree but not much else. Boxing, in general, seems to be highly resistant to both change and regulation. For over a hundred years, fighters resisted wearing gloves at all. And since then, they have thwarted most efforts at innovation. The movement to remove the thumbs from gloves, for example, has only succeeded in a few areas. Gloves have become more heavily padded in recent years and the padding materials themselves have grown more resilient, but many experts insist that this simply allows fighters to punch harder and inflict more damage
- Mike SMITH
Comments 0